HDPE deep drying technology
Contact us
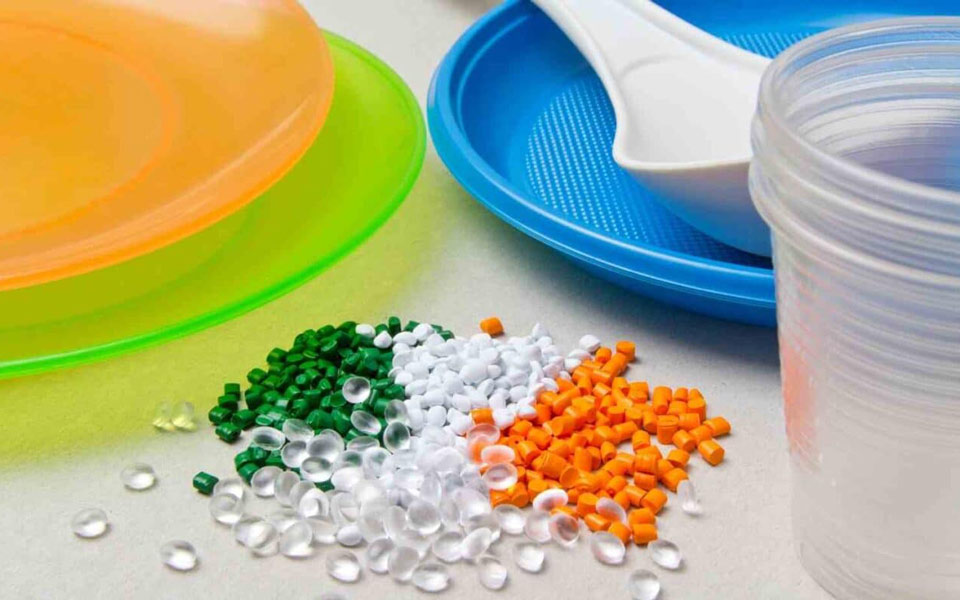
Our fluid bed dryer drying process can complete the drying in HDPE production more efficiently.
The wet HDPE materials from the upstream system evenly enter the upper part of the first stage of the fluid bed dryer dryer and come into contact with the hot nitrogen gas from the lower part to fluidize the HDPE powder. The first stage of the fluid bed dryerdryer is equipped with four chambers and steam heaters. During the fluidization and movement of the materials, the hexane contained in the HDPE powder is continuously evaporated. Part of the heat required for evaporation comes from the hot nitrogen gas, and the other part comes from the built-in steam heaters. The hexane vapor and some dust generated by evaporation are discharged into the first-stage cyclone separator from the upper part of the first stage of the fluid bed dryer dryer along with the drying carrier gas.
The first-stage fluid bed dryer serves as the material mixing area of the system. No built-in heat exchanger is installed in the feeding area so as to fully mix the materials, and hot nitrogen gas is injected to prevent the materials from caking and the shell from scaling.
The pipeline from the exhaust outlet at the top of the first-stage fluid bed dryer to the air inlet of the first-stage cyclone separator is equipped with steam tracing to prevent dew condensation. The heat source medium for the steam tracing is low-low-pressure steam.
A certain proportion of maintenance manholes are set in the wind chamber of the fluid bed dryer, and a bottom discharge port is arranged at the bottom to facilitate the cleaning and maintenance of the equipment.
A certain proportion of sight glasses, temperature transmitters, samplers, etc. are installed in the fluidization section to facilitate the observation of the running state of the materials.
An air suction shell is set at the top of the fluid bed dryer. The height of the shell meets the sedimentation requirements of the powder and reduces the entrainment amount of the materials. The air suction shell is equipped with maintenance manholes to facilitate equipment maintenance.
After being dried in the first stage, the HDPE powder enters the second stage of the fluid bed dryer dryer through the overflow weir at the bottom of the first stage. Here, the hot nitrogen gas fluidizes the HDPE powder, and the process is similar to that of the first stage of drying. The heat required during the drying process is mainly provided by the built-in steam heaters. After being dried in the second stage, the moisture content of the HDPE powder reaches less than 1% and enters the subsequent system through the bottom overflow weir of the second stage and the discharge rotary valve at the outlet of the dryer. The fluid bed dryer is equipped with two discharge ports. One is the bottom discharge port above the air distribution plate, which is used to discharge large pieces of materials or empty the material layer. The other is the top overflow port under the normal fluidization state of the materials. When the material layer is stable, the materials are discharged by normal overflow.