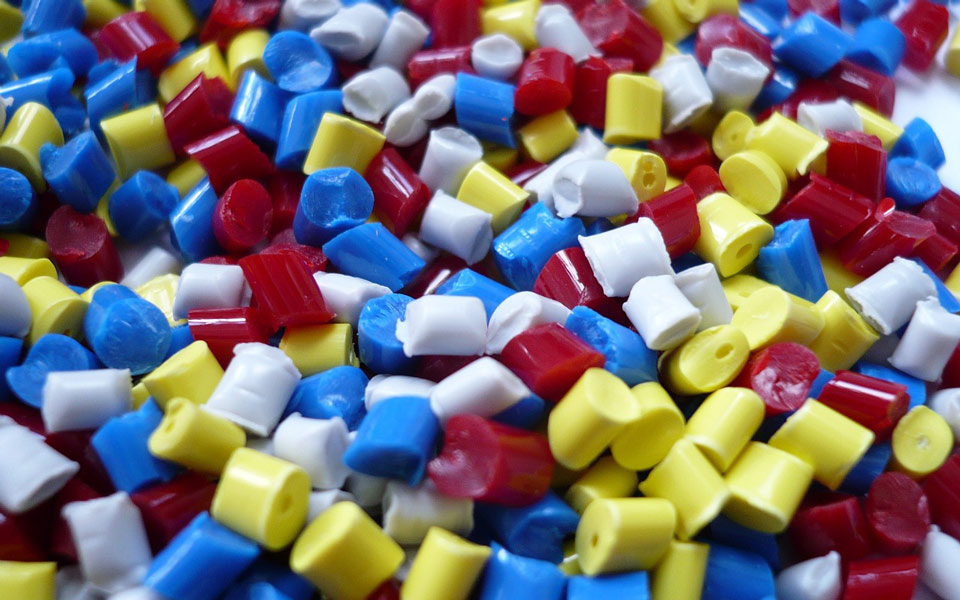
-Salification
Dissolve adipic acid and hexamethylenediamine in water respectively to form aqueous solutions, and then mix and neutralize them to obtain the nylon 66 salt solution.
-Polymerization
Pressurized aqueous solution polymerization: In the early stage, pressurized aqueous solution polymerization is adopted to prevent the volatilization and decomposition of monomers. The nylon 66 salt solution is concentrated in an evaporator, heated in a preheater and then fed into a reactor. Pre-condensation polymerization is carried out under certain pressure and temperature to obtain a prepolymer with a degree of polymerization of about 20.
-Melt Polymerization
After the prepolymer enters a flash evaporator for pressure reduction, vaporization and dehydration, it enters a post-polymerization reactor. Under the action of a screw propeller, a thin film is formed, and water molecules are further removed so that the relative molecular mass of the polymer meets the process requirements and the condensation polymerization reaction is completed.
-Pelletizing and Cooling
The nylon 66 resin after the polymerization reaction is cut into pellets by a pelletizer. After pelletizing, it needs to be cooled rapidly to avoid adhesion of the finished products.
-Post-treatment
It includes steps such as drying and plasticization. Since nylon 66 is prone to moisture absorption, drying treatment is required to control the moisture content. Adding plasticizers can improve its toughness and ductility to meet different application requirements.